The cobot story is, in many ways, the complete opposite of conventional pre-2010 industrial automation. Cobot automation focuses on the end-user, aiming to provide simple, safe, user-friendly, and low-cost entry to industrial automation.
Industry media is full of cobots; there are many examples of real wins and opportunities, but some big hyperboles and myths are routinely pushed. This article will cut through the hype to offer the proper balance between cobots, robots, and many inter-playing factors.
Cobots are a significant breakthrough for industrial automation, but the biggest advancements come not from the technology but from wider industry changes:
- Made automation less daunting for small and medium enterprises.
- Pushed the industry players to place emphasis on the end user and simplification.
For growing SMEs, the biggest obstacle to automation is often confidence, which is where cobots can help. In many cases, the investment in industrial automation makes sense economically, but fear and lack of confidence limit companies from making that leap. Stakeholders can now be introduced to a much less daunting cobot system as the first step of automation.
Beyond the cobot technology, all manufacturers have placed a large emphasis on training and demystifying the skills into bite-size chunks. For example, technical details prior represented as electrical drawings are initially shown as pictographs. Graphical programming reduces the otherwise overwhelming learning curve for beginners.
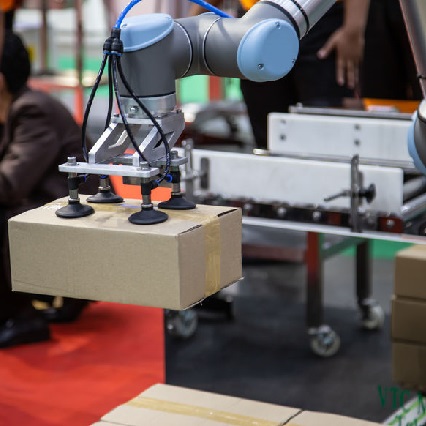
To experienced robot engineers, cobots are actually no simpler to integrate; arguably even more difficult due to limited features, but it takes experience to reach that level. In the robot field, cobots are also a great teaching aid for beginners because all the same concepts are present.
Cobot and Robot Reality
While cobots have opened opportunities, the marketing narrative has also pushed historic connotations on “conventional” industrial automation and robotics. The overwhelming narrative from dedicated cobot manufacturers pushes the 1980s picture of industrial robots and is not at all a true sense of state-of-the-art. You will clearly see a difference if you compare the marketing story of dedicated cobot manufacturers, and major players who produce both cobots and robots.
If you’re going to take one thing away from this article, it is to understand Cobots do not replace Industrial Robotics; but Cobots and Robots complement each other.
In the hype that surrounds Cobots, it is often missed how industrial robotics have also greatly advanced; and offer just as wide opportunities that are yet to be dreamed. What is often overlooked is how smart the modern units have become and all the available features that can be included for minimal cost. Even from the mid-2000s till today is a quantum leap in your robot package. Slaving away on a factory floor with my industrial-focused PhD work around 2008, robot technology was frustrating limited, whereas today, you’re only limited by your imagination.
The below table shows a high-level state-of-the-art comparison between cobot and robot systems. The technical details will be expanded in a later article to give a more in-depth comparison and explain the subtle differences. Removing the spin, the user and safety differences between cobot and robots is much closer than most realise.
Modern Robot | Cobot | ||
---|---|---|---|
Intrinsically Safe | No | No | |
Possible Safety Modes | Separation, Coexistence, and Cooperation | Separation, Coexistence, Cooperation and Collaboration | |
Hand Guidance | Optional | Yes/Optional depending upon the manufacturer | |
Programming Method | Code + Graphical depending upon the manufacturer | Code/Graphical | |
Skillset | Beginner/Professional/Expert | Novice/Beginner |
The spider figure below is very good at demonstrating the complementing relationship between the two technologies. The figure has been arranged with opposing attributes opposite; such as speed vs safety; or simplicity vs intelligence. Achieving one attribute is easy; succeeding at both requires much more experience and innovation. What is very clear is how cobots have offered attributes not previously given emphasise by key players.

The big change yet to be seen is the impact of established robotic manufacturers fully integrating cobot technology. The recently released FANUC CRX series and some rumoured new ABB Cobots will be another big change in the cobot/robot world.
The big robot manufacturers have been producing robots for six decades and have all the got all classical elements to a very fine art; but they did get caught off guard by cobots entrants. These companies have the billion-dollar R&D budgets and technical knowledge to leapfrog early entrants. If you take FANUC CRX or new ABB units these are actually more towards a full convergence of cobots and robots.
When to Consider a Cobot for Automation
The big opportunity cobots provide is the economics of retrofitting automation into manual operations and the flexibility provided to SMEs. This distinction for brownfield sites is important for cobot applications; it can lower the initial barriers and is a pragmatic first automation step.
The big returns from cobot automation come from the following use-cases
- True collaborative applications
- Integrating into existing production lines
- Mobility around the factory floor
True Collaborative Applications
The technical definition for “collaborative” applications is the “robot” and person working in the same space, on the same product/task, at the same time. True collaborative applications are very rare; think of a person assembling electronics and then guiding a cobot to fasten the screws while assembling the next unit. Most “collaborative” systems demonstrated in marketing actually come under the technical definitions of coexistence or cooperation. These applications have much more flexibility, and many more options could better suit your operation. This will be covered later in a technical slanted article.
Retrofitting Cobot Automation in Manual Production
Cobots provide the opportunity to automate existing production processes without widescale rejigging of a production facility. Sometimes an existing facility has one key bottleneck that is transformational when solved by fixed or robotic automation. What is more common with a brownfield site is a range of bottlenecks that are inherit to the facility that won’t allow a significant throughput increase.
Designing a production space from scratch allows a process flow and layout to suit automation. Unless you talk about a massive corporate integrator, there will be a negligible cost difference between a cobot or robot solution on a clean sheet install. Then head to head, rarely can a cobot remotely compete with a Robot on pure ROI.
On a clean site, a robotic system will attain a much higher ROI from the increased production rate, production continuation from higher system intelligence, plus longer lifetime and extended service intervals. Designed with modern safety in approaches in mind, a robot solution will allow a similar footprint to a cobot option.
The equation is different in a handcuffed brownfield site; the flexibility to arrange the facility to suit safety systems and remove inherited bottlenecks doesn’t always exist.
Modern safety systems are highly advanced; these feature numerous electronic means of detecting human encroachment and providing protection. However, due to the incredible speeds and forces from robots, effective electronic safeguards require minimum response times and clearance distances; these can be problematic to crowbar into existing spaces. A robot solution may be impossible to retrofit into a production facility, or it can, but the robots are slowed down towards a cobot to ensure safety.
Cobots can offer a good fallback option even when not an actual collaborative application.
- The collaborative safety features can be a backup option when the more efficient external safeguards don’t fit a brownfield site.
- The slow cobot speed will not negatively impact the production rate since other bottlenecks still exist.
The flexibility of Cobot Automation
The ability to move a cobot around a facility provides good flexibility to suit flexible manufacturing. This can be very beneficial to small companies where the automation cost for one cobot can be used across multiple tasks.
There are two factors to this flexibility
- The ease of repurposing a cobot
- The difficulty of moving a robot
Moving a robot around a facility is entirely possible; however, each location will probably require some form of permanent nest. This is not a question of cobot or robot safety technology but the physics involved with a robot. Robots provide much higher speeds and accelerations, and compounding that, robots are built much more rigid and, therefore, heavier. The forces involved require some significant engineering to keep them attached to the ground unless a robot is limited to a cobot speed. You’ll not mount a robot on a self-contained moveable trolley unless it operates slowly.
The second issue with moving a robot is that the safety system should be completely revalidated each time the kit is reassembled. This validation needs to be conducted by a “competent” person. A cobot should also be revalidated for each move, but if you’re not disconnecting safety hardware nor using external safeguards, then checks can be minor in comparison.
Cobot Automation Mistakes
Believe Cobots are Intrinsically Safe
This is the big one and rarely do you see the record set clear by cobot manufacturers unless pushed by a technical audience.
Cobots have numerous safety features and attributes that make them possibly safe; but the overall system defines the safety outcome.
Take the following far-fetched examples to picture how the application, not the cobot itself, defines the safety outcome.
- A cobot with a knife attached.
- A person standing between a cobot and a furnace
Beginners often blindly follow the marketing narrative without paying much attention to the fine print nor fundamental machine safety concepts. Visiting tradeshows, even most cobot demonstrations, would not meet the safety standards and technical specifications. Time and time again, you’ll see the common mistakes of not factoring in related workspace hazards and crush points, region of human contact, and factors such as sharp edges on grippers or held products. It commonly takes the two ridiculous examples above for the inexperienced “click” and start fully understanding their responsibilities.
Developing an application’s holistic risk and hazard view is one of the first tasks that should be done with any industrial automation, cobot automation included. Viewing safety as an afterthought to consider just prior to production is a common mistake, even with many by machinery companies.
Not following machine safety concepts from the initial steps can lead to the following outcomes:
- Cobot installations unknowingly pose an unacceptable risk to operators.
- Unfortunately, operators will also often not question the risk
- Remedial work to fix safety is often destructive to the original purpose and ROI of the system.
- What typically happens is extra electric safeguards and/or guarding must be added, and the outcome is basically installing a cobot as a robot with a greater final cost and less performance.
Not Factoring ROI
Every application is different but a robot will normally have a production output of 2-5 people; a cobot on the other hand will often struggle to match a sole person. A cobot is simply not going to match a tuned robot or mechanised system for production rate.
Cobots are really best suited to support roles rather than direct labour replacement. Cobots can be great for increasing relative production from a person who completes multiple tasks. Supportive functions can be achieved such avoiding machine wait times, or left to plod along at simple tasks while human has higher priorities.
Sanity checking is required to ensure a cobot is the correct solution; take the following CNC example between a cobot and robot implementation. A robot will be faster, but it depends upon the CNC cycle time if the overall impact is significant. An important note with machine tending applications is you shouldn’t need a new program per part,
Production Type | Machining Time | Cobot Load | Total Cobot Cycle | Robot Load | Total Robot Cycle | Relative Robot Increase |
---|---|---|---|---|---|---|
Complex Parts | 180 | 15 | 192 | 5 | 185 | 4% |
High Part Volume | 40 | 15 | 55 | 5 | 45 | 20% |
Its Not About Coding
To the beginner dropped into the world of robotics the sight of programming is a daunting experience. The actual critical skills for both industrial robots and cobots, understanding the motion concepts, figuring out an automated process, and problem-solving all the little intricate details that humans solve subconsciously.
A graduate engineer can program a robot easily, but it takes years of experience to become proficient with all the real-life problems above.
Programming is really only converting that problem into a language a machine understands. Even the highly featured languages from ABB or Kuka are on the very simple end of programming languages; languages from FANUC, Kawasaki, Yasakawa are completely prehistoric. Even with cobots, once the concepts are understood, novices will often move to text programming relatively quickly.
Cobots will sort all you problems
One key lesson for anybody starting with automation is there are numerous drawbacks compared to a person. Typical high SKU counts should not be a significant problem to any professional engineer in the Industry 4.0 world. Inconsistency and variation of incoming materials still is the archilles-heel to automation.
Human labour has the ability to subconsciously adapt to all sorts of variation due to sight, touch; and to problem solve on case by case basis. Automation system can handle variation but it will come at the expense of cost, complexity or rate;
Guarding is Not Evil
A company heavily focused around the idea of not wanting to use fixed guarding is the sure sign that all their knowledge has come from cobot marketing. There are good intangible benefits to avoiding fixed guarding such as ease of access, flexibility, and asthetics etc. The reality is; the simplest, best performing and cost effective automation solution, will generally use fixed guarding were possible.
Automation can handle variability, but it will come at the expenses of rate, complexity or cost. The number one source of variability in a production line will be human labour. That is not meaning malicious intent; but all the subtle things a person could unconsciously do differently, and different operator habits.
The best way to avoid variation is to physically control how humans can interact with the automation system. In many automated systems, safety will be linked to the doors being closed; but the electronic lock on the doors will controlled not to provide safety, but to control when an operator is allowed access.
Comments are closed