How to correctly apply an industrial vision system to an application and return value is often misunderstood. Not just at the end user operation space, but even at the professional general automation level. Industrial Vision systems tend to be seen as a magical silver bullet to solve all problems or disregarded without proper consideration due to lack mastering the technology and potential solutions.
Understanding the benefits and how to factor into your operation to extract these is key to achieving a highly valuable outcome or just an expensive white elephant.
Capturing Value with Industrial Vision System
To capture returns from a vision system you need to understand how these systems add value and offer efficiency to your operation. In this series of articles covering machine visions systems we will explain what these systems can offer, and how to correctly consider for your operations.
We briefly mentioned the guide to mastering vision system in our Dec article of NZ manufacturer, and will expand on some of the deeper technical capabilities in a later article. Our technology page covering machine vision can also serve as reference.
Industrial Vision system can be used across a range of industries and purposes, in general covering such as presence detection, guidance, gauging/measurement, general data collection, and the slant for this article quality control. The benefits from industrial vision systems roughly fall into three categories.
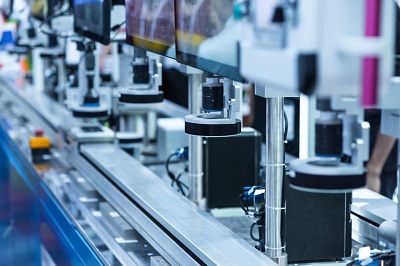
Operational Efficiency Improvements from Vision Systems
Labour Reduction, Scale Operations, Maximising Production Output
Vision systems offer the efficient use of labour, and by removing choke points, the ability to consistently maximise equipment throughput. Manual QA is not a highly skilled task; but a role neither the less that requires training and experience to achieve consistency and speed. This learning dead-time poses a challenge when it comes to increasing staff for scaling operations, and is particularly problematic if you rely upon casual or seasonal labour. Even with experienced staff, human inspection is a common bottleneck and one that will rapidly fall apart if pushed beyond the limit.
A vision system will significantly faster perform a detailed consistent measurement and do so independent upon the product quality. The first point is easily comprehended but being independent upon product quality is normally a bigger benefit to local operations. The rate of human inspection is highly dependant upon the quality of items; bad products require additional time to check and therefore your production lines slow down.
Primary or secondary industries have time/batch variability and therefore the production rate and/or staff count will also be variable to match. To handle this variability either staff are kept in reserve wasting money; or production needs to be below full capacity to provide a safety margin. A vision system does not care about the quality and runs at constant rate. Taking that a step further, if the next bottleneck is post the vision system, then production output can be keep consistent and the only variability is the amount of rejected product. Production managers of manual lines can only dream of that capability.
Value Recovery Opportunities from Vision Systems
Labour efficiency is the leading driver for approving the investment in a vision system; at least in a company’s first step. In practice, and in all applications, I have ever encountered, the extra value recovered and reduced waste, dwarfs the labour saving.
Initial gains upon installing vision system will stem from the improved quality assurance and reducing leakage of waste throughput manufacturing process. Product recalls are minimised by 24/7 consistent electronic QA identifying faulty products prior to shipping. If recalls do happen then there is detailed traceability and records for targeted action. Mid-process faults are identified early reducing resource waste and production capacity on unrecoverable units. Catching these faults early also reduces the possibility of equipment damage and lengthy downtime.
The big transformational changes to efficiency and profitability come when the vision system moves beyond a simple labour aid. Consistent accuracy and real-time visibility provide confidence to reduce safety margins within manufacturing operations. These tolerances being in the form off oversupply and commonly known as “give away”. World-class manufactures will also feed this back to engineering teams for continuous improvement gains by becoming more aggressive at the design stage.
Another rarely considered benefit is that the value of your products can increase purely from the tighter QA control. This happens in many primary and secondary industries where wholesalers or retailers will pay a premium for product that has been subjected to state-of-the-art QA. You need to be aware on the other side of the fence is your products may suddenly be locked out of certain markets or penalised if you don’t use these systems. This has been widespread practice for many years in manufacturing and horticulture; and now some opportunities and concern for others within agri and aqua-culture related industries.
Operational Flexabilty from Vision System Integration
Vision systems offer the ideal solution for flexible low volume, high variability production. Vision system allow intelligence and guidance behaviour in a production line reducing the need for complicated mechanisms and bespoke engineering. Real-time intelligence is one of the key attributes that defines the leap between mechanised and automated systems.
Conventional production lines have numerous custom mechanisms tailored to each production part. These custom structures incur considerable design and build expense to cover bespoke machine components. In high mix and flexible manufacturing this poses a challenge since the smaller production volume of each specific does not outright pay for machinery; and therefore, machinery needs to be multi-purpose. Multi-purposes machinery becomes incredibly expensive with custom jigs and fixtures for each part, and a swath of adjustments that can be cost prohibited to automate or time-consuming and troublesome for manual change over.
Many of those involved with such machinery are indeed highly skilled and experienced; but having multiple one-off components also means issues with reliability, maintenance, and service headaches over the equipment’s lifetime.
Vision system technology will not be the correct choice in all applications, but it allows production lines to move toward generic standard equipment and more modular future proof layouts.
Instead of engineering specific fixtures to align parts, the parts can instead be identified on a simple conveyor belt and guidance sent a robot; plus you could integrate QA. Rather than designing and building new jigs, possibly reconfiguring the line for new production items; some trial parts could be quickly tested, and the vision system given an additional program. Change over of production runs becomes simpler and quicker with reduced physical changes. Manual mistakes can be avoided with automatic switching of vision programs connected to MES systems (Manufacturing execution system). When your integrator is highly skilled they can also have the vision system check for incorrect manual configuration at run change; many recalls could be avoided if this is implemented correctly.
Manual Quality Control
Before diving deeper into how vision system capture value, firstly consider human based quality control approaches and the challenges faced.
Sample Based Quality Assurance
A common method of manual quality control is using a sampled based approach were 0.1, 1 or even 10% of products are evaluated. This limits the cost of the quality control; however, it has one major drawback in that it assumes failures are random.
In practice anybody away from the accountancy office knows that is not how failures present themselves. Often there is a intermittent malfunction, temperature fluctuation, or a batch of poor materials somewhere in the production line and you get a chain of faulty products. Sampling for quality control you run into two problems. Small, medium, or intermittent faults are often never detected until delivered to the end customer. On larger faults you may get lucky and happened to find the failure quickly, but most times a significant amount of production has been wasted before the fault is identified.
100% Inspection
Automation as this article discusses has opened many opportunities for 100% inline section, however, historically two types of products have been manual inspected to this extend.
- Complete inspection is common on high value products or products that cannot afford failures such as healthcare/aerospace. The product value or competition equalling regulatory requirements in these industries therefore supports the expensive quality control process.
- The other application is relating to handling highly variable natural products in both the primary and secondary industries, both common in NZ and Australia. Having natural products means the defect rate in such industries is so high it is a necessity to inspection each and every product. This creates a challenge for developed countries since the material unit cost is often low and therefore the human labour component becomes a significant portion. In a global market that sets the product value, the added labour cost cannot be recovered, and this is a straight loss of margin.
Human Inconsistency
The other downside to human quality control is the consistency of the inspection; this is particularly troublesome in our primary and secondary industries. In these industries quality control is often subjective and makes the scope for inconsistency of human judgment even wider.
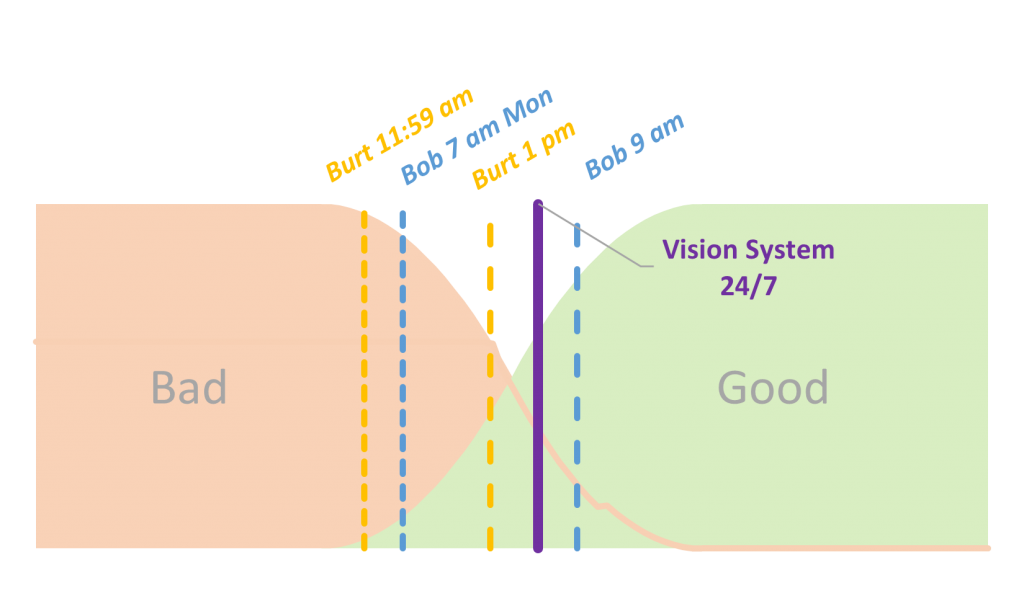
As someone who has spend over a decade on highly advanced, and many patented, vision systems the above is situation that plays out time and time again. When a vision system is installed, you often end up in a discussion with the end users operations team how the machine results are differing from the human quality control. This is actually when the lights start to fully go on for the operations team.
During trials and commissioning you constantly run blind tests, and unknown to the manual QA team give them the same parts numerous times and compare to the machine results. So part you are saying is graded incorrectly, has been through your QA various times with various gradings yet the machine has instead run consistently. The cut point of the machine may need fine tuning, but that is often the first time that operation has had extensive of repeatability, and the human variation has just be laid bare.
Vision System Opportunities
A number of levels of automated machine vision system are out there; on the simplest end of the spectrum you have barcode and colour chart readers on packaging, gauging for checking bottle tops, counting and confirming items such as blister packs, and scoop detection in infant formula or washing power etc.
It gets more complicated when you go beyond the ordinary and towards the primary and secondary type industries common to NZ and Australia. There is a vast array of opportunities in these industries that are not captured. As you go from the run of the mill application such as gauging bottle caps, the vision expertise becomes critical and it almost seems like a dark art unless you totally understand optical physics, in-depth knowledge of equipment, and computer science. Even advanced industrial automation teams struggle with technical knowledge to solve primary and secondary industry challenges, or academic and research institute tend to have the technical knowledge but not the commercial nous to deliver pragmatic solutions outside the lab.
The Secret of Machine Vision System
The most important factor that needs to acknowledge in your overall operation is there is always a grey area to vision systems or any form of measurement. This is true for both manual and automated, and it is there even you do not know, or don’t want to know about it.
This factor is that is often met with trepidation, but this is the critical element to be understood by all if you want to be world class. Sticking your head in the sand or pretending it does not exist and your project could be doomed, and at best you’re leaving a competitive edge on the table.
The value provided by a vision system is driven by that grey area of measurement. How large that grey area is, what factors can influence that grey area, and most importantly how to tailor your operations to work in with that grey area.
Understandably many want the world to be black and white; but understanding that grey region lets the system operate much more aggressively capturing more value, and the visibility to correctly focus improvements.
Comments are closed